Automation of Mobile Grain Dryer in Chernihiv Region
In October 2013, one of the farms in Chernihiv region, which specializes in drying grains, approached our specialists for help in automating their mobile grain dryer.
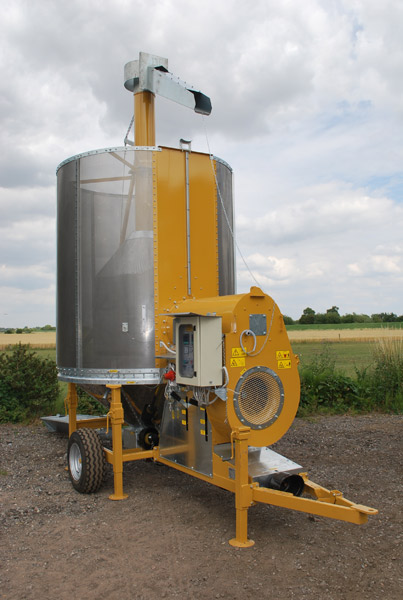
Principle of Operation of the Grain Dryer
The principle of operation of this grain dryer is as follows: the grain is loaded into a container, where warm air is supplied through a side pipe. Inside the container, there is a vertical screw that rotates and mixes the grain. The dryer is equipped with an 18.5 kW motor (with an actual consumption of 17.5 kW), which operates on the star/delta principle to ensure a smooth start with a constant speed.
Modernization of the Grain Dryer
The main idea of the modernization is to reduce the rotation speed of the screw during drying, which provides a slower passage of grain through the zone of warm air. This allows for increased drying efficiency in one pass. To implement this solution, it was decided to install a frequency converter.
Results of Frequency Converter Implementation
After installing the 18.5 kW frequency converter produced by Delta Electronics series B and activating the energy-saving function, significant results were achieved:
- At a frequency of 50 Hz, the electricity consumption was 12.5 kW.
- At a reduced speed of 23 Hz, recognized as optimal for drying, consumption dropped to 4.3 kW.
- The speed of drying the grain decreased by 20%.
With the electricity tariff of 1.92 UAH, the savings amounted to 1.92 * (17.5 - 4.3) = 25.3 UAH per hour. Over 1000 hours of operation (42 days), the savings totaled 25,300 UAH, which fully covered the implementation costs and increased the amount of dried grain per day by 20%. Furthermore, the percentage of damaged (broken) grain was reduced. The frequency converter ensured a smooth start of the motor, which reduced the load on mechanical components.
If you are interested in this implementation, please contact our specialists for detailed consultation by visiting the Contacts section.