Energy Saving of Induction Motor with Squirrel-Cage Rotor
The question of energy saving in an induction motor with a squirrel-cage rotor constantly arises, especially when it operates at nominal speeds. In this case, the motor consumes a certain current, which, in principle, would remain unchanged even without special adjustments. However, recently many manufacturers of frequency converters have implemented features known as automatic energy saving or automatic energy optimization. Typically, this function is disabled in factory settings, as its effective use requires appropriate load conditions for the motor across the entire speed range, including low frequencies up to 15 Hz.
The energy-saving function adapts the output voltage to the alternating current load, which, in turn, reduces the acoustic noise of the motor and energy consumption. For this function to work correctly, it is necessary to accurately set the motor parameters, including the power factor (cosφ). Sometimes the function for automatic determination of motor parameters is used for this. It is noted that energy saving is particularly effective in vector mode and also for loads that do not change frequently.
Example of a Real Object
Let’s consider a real case: the drive of a stone crusher at a quarry. The crusher drive operates at a frequency of 50 Hz. If the motor is connected directly to the power grid, when the load changes on the conveyor, the motor current changes while the voltage remains at 380 V. However, with activated automatic adjustment of motor parameters, vector control, and energy-saving function, the current changes proportionally to the load, and the power supply voltage to the motor is adjusted. In practice, this can provide energy savings of up to 35% when operating this mechanism.
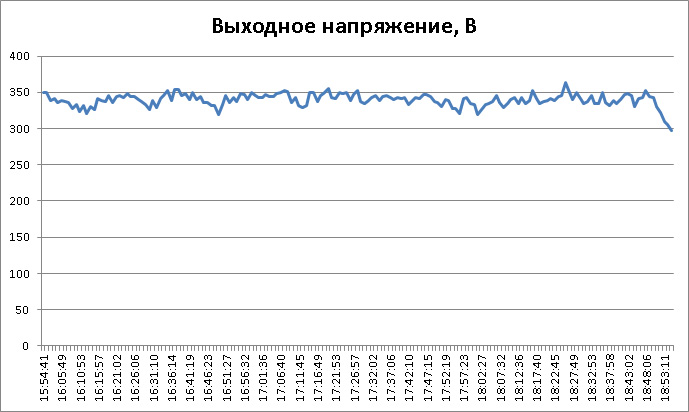
The graph shows that the voltage at the motor does not exceed 350 V, which is the essence of the energy-saving function. In this case, the average annual savings amounted to 23% of electricity, leading to the payback of the solution for a 75 kW motor in just 15 months, even considering the night tariff.
Conclusion
Thus, the automatic energy-saving function is indeed effective for drives operating in nominal mode. The overall efficiency of the system is approximately 95-98%, and the share of reactive components is minimal. If you need more detailed information, you can contact our specialists in any convenient way in the Contacts section.