Energy Savings by Replacing an Electric Motor with a Synchronous One
Replacing the constant-speed fan electric motor with a synchronous motor with variable speed and an ACS880 drive (VFD) allows for significant energy savings of up to 50% at a load of 75 kW.
Overview of UFA's Mill
Since 2011, the mill on the UFA company's farm, which produces poultry feed, has been one of the few automated mills in the world. The mill, built in 1965, operates without maintenance personnel from 9 PM to 5 AM.
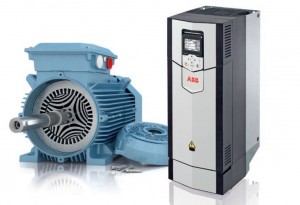
Mechanical engineer Peter Hofer, who is a member of the management team at UFA, is responsible for all production at the modern UFA farm. He notes, "Efficient energy use is possible if the technological processes are analyzed correctly."
Motor Replacement and Process Optimization
Together with B&H Technology Group, UFA has managed to optimize processes at the Sursee feed plant. Investments in new technologies quickly pay off due to energy savings. In 2015, a 75 kW drying fan was installed that draws air from the tenth floor of the production tower. Previously, ventilation was controlled through an automatic switch, and the motor always operated at maximum fixed speed.
Despite the modern state of the equipment installed in the 1980s, the need for replacement arose. Peter Hofer met with experts from B&H to discuss opportunities to enhance efficiency by upgrading the ventilation system with an ABB drive and utilizing a high-efficiency synchronous motor. As a result, a synchronous motor was installed, controlled by a new ABB ACS880 frequency converter.
Results: 50% Energy Savings
The ventilation system has demonstrated excellent results. It operates five or six days a week around the clock throughout the year. Thanks to this system, around 300 megawatt-hours of electricity have been saved, which has also led to a significant reduction in CO2 emissions. Among the additional positive aspects are the lack of need for cooling the control cabinet, increased space, and savings due to the smaller size of the motor.