Articles
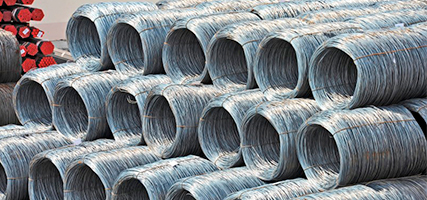
WHAT IS AN AGING INFRASTRUCTURE AND HOW CAN YOU PLAN FOR IT?
Aging Electrical Infrastructure: Challenges and Solutions
Outdated electrical infrastructure can lead to serious problems at your facility. It is important to timely identify and address these issues, as older equipment is more likely to fail and require repairs.
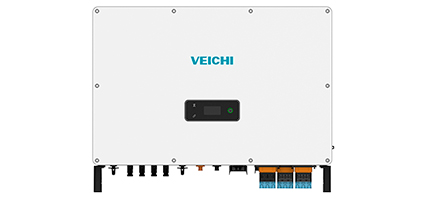
Difference Between Hybrid and Grid-Tied Inverters
Choosing a Solar Energy System: Hybrid and Grid-Tied Inverters
When selecting a solar energy system, it's important to understand how different types of inverters work. The two main types are hybrid and grid-tied inverters, which have different functions and purposes.
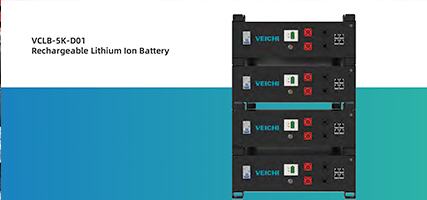
What you need to know when choosing a LiFePO4 battery
Lithium Iron Phosphate Batteries (LiFePO4): What You Need to Know Before Buying
Lithium iron phosphate batteries (LiFePO4) are gaining popularity due to their high energy density, long lifespan, and safety. However, before purchasing such a battery, it is worth paying attention to several important aspects that will help you make the right choice.
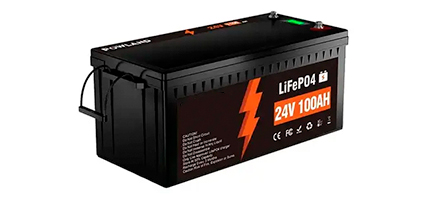
LiFePO4 Batteries for Hybrid Inverters
LiFePO4 Batteries for Hybrid Inverters
Lithium iron phosphate (LiFePO4) batteries are becoming increasingly popular in systems with hybrid inverters due to their numerous advantages.
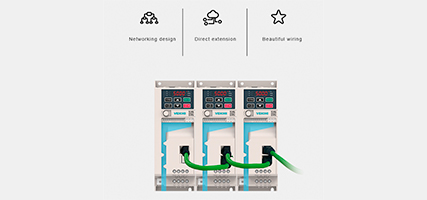
Main use cases for VEICHI AC10
VEICHI AC10 Frequency Converter
The VEICHI AC10 frequency converter is a high-efficiency device that allows for the regulation of speed and performance of electric motors across many industries. This device provides smooth starting, stopping, and speed control, leading to reduced wear on equipment and improved energy efficiency.
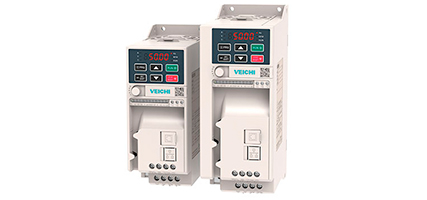
Frequency Converter VEICHI AC10
VEICHI AC10 Frequency Converter
The VEICHI AC10 frequency converter is a reliable and efficient solution for controlling the speed and power of electric motors. This device is designed for use in various industrial sectors, including manufacturing, water supply, HVAC, and other industries.
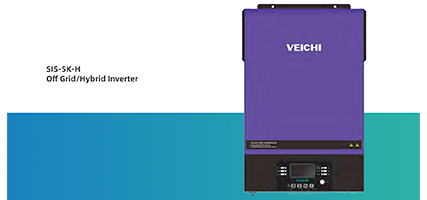
The VEICHI SIS-5K-H 5kW hybrid inverter
Hybrid inverter VEICHI SIS-5K-H 5kW
The hybrid inverter VEICHI SIS-5K-H with a capacity of 5 kW is a modern and reliable solution for effective energy management generated by solar panels. This device allows the integration of various energy sources and battery systems, contributing to reduced electricity costs and increased autonomy of your energy system.
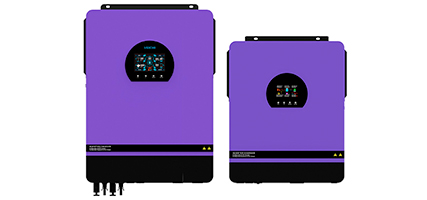
Powering an Apartment with a VEICHI Hybrid Inverter
Connecting an Apartment to VEICHI Hybrid Inverter
Connecting an apartment to a VEICHI hybrid inverter provides reliable and efficient power supply by utilizing energy from the grid as well as from solar panels or other sources. In this article, we will discuss the main steps that need to be taken to organize such a power supply.